
Organic, Light and Resistant: Thermoset Technology In Architecture | Construction Buzz #226
)
Initially created for aerospace purposes, materials based on advanced fiber-reinforced thermoset technology are increasingly being considered not only to manufacture specific building elements but also to change the way buildings are conceived, designed and built. Despite being incredibly resistant –almost six times stronger than steel– fiber-reinforced materials are light and easy to handle, allowing the creation of complexly shaped but efficient architectural projects.
We spoke with experts from ShapeShift, the creators of the ShapeShell product, in order to deepen our understanding of this technology and learn more about how we can take advantage of its possibilities in our future projects.
In combination with advanced fibers, a thermoset resin allows the creation of light-weight organic shapes. Lighter than traditionally recognized structural materials, this material offers lower transport and installation costs, the latter of which can represent up to 50% of the total cost of materials. A fully integrated advanced fiber-reinforced structural assembly reduces the reliance on multiple contractors and removes the need for a crane or other heavy hoisting equipment, as would be required for an equivalent system such as prefabricated concrete planks.
A building built of advanced fibre-reinforced elements can also provide increased protection against extreme environmental hazards such as earthquakes, during which lighter buildings are less likely to suffer structural damage than their heavier steel or concrete counterparts.

There are two ways to assess the future of advanced fiber-reinforced materials in architecture. The first way is to view them as materials that can be substituted for traditional construction materials which will improve building performance through the replacement or re-engineering of specific building elements that benefit the properties of the advanced material.
Secondly, advanced fibre-reinforced materials can be seen as offering completely new possibilities for the way buildings and public artwork are conceived, designed, engineered, fabricated and constructed. Thus allowing a new way of building for the digital age by incorporating 3D design and CNC mould making technologies.
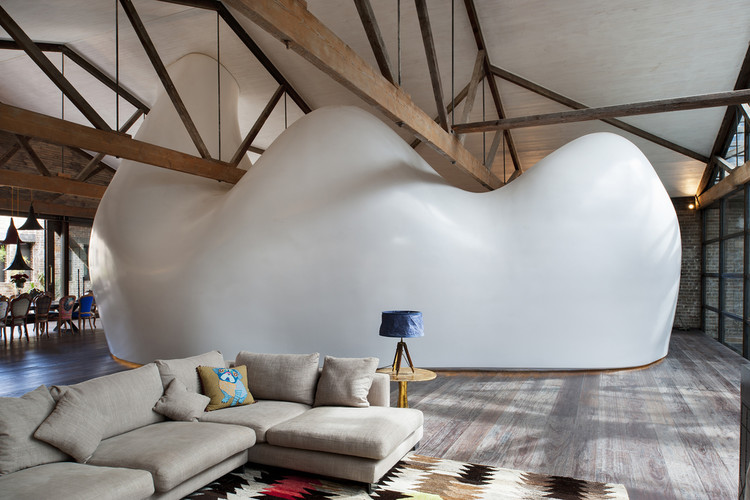
Applying aerospace manufacturing techniques, allows ShapeShell to exhibit unique and consistent structural properties that cannot be achieved with traditional isotopic materials. Resin vacuum infusion involves laying tailored reinforcement fabrics into layers into a mold, sealing the fabric stack under vacuum and introducing the resin that infiltrates through the reinforcement. The result is a self-supporting shell molded from the complex mold shape.
Thereby, carbon fibre-reinforced substrates are almost six times stronger than steel –the industry favourite– in terms of tensile strength and potential spanning distances. Also, they have a low maintenance surface finish, simplicity of installation, being chemically resistant to corrosion and having dimensional stability.
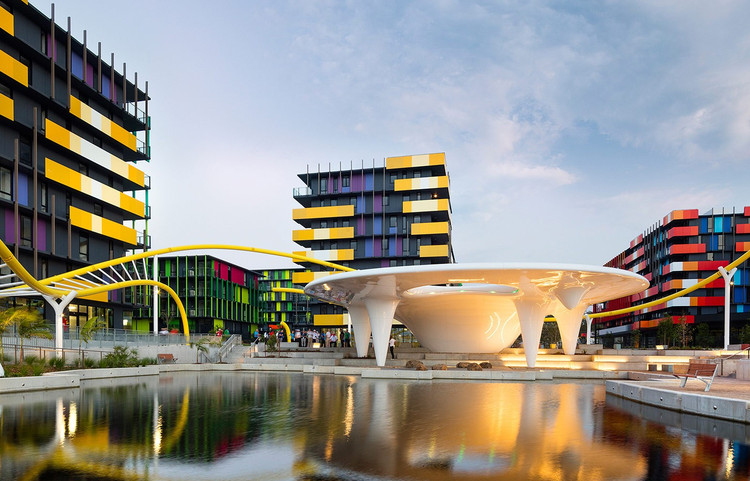
While advanced fiber-reinforced substrates are typically more costly than steel or equivalent structural elements on face value, their high initial cost can be reduced when considering their other cost-saving characteristics over the lifecycle of the product.
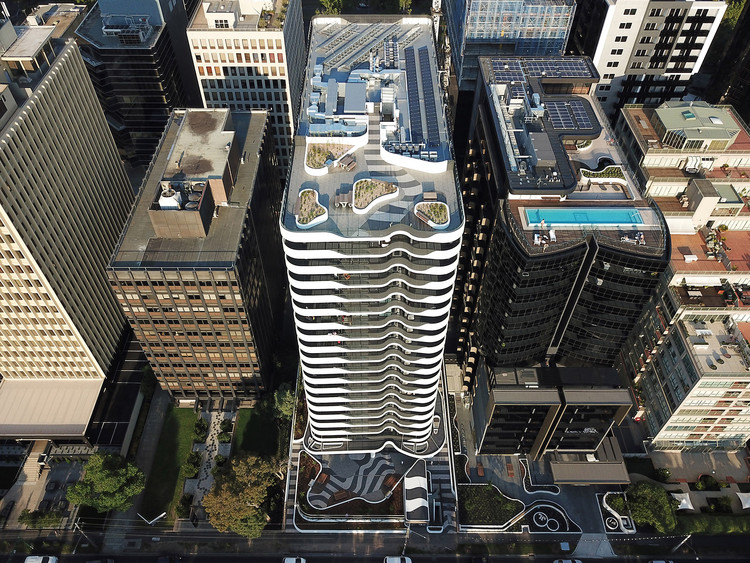
Due to the lightweight natural of the material, the support structure is usually minimal.
Reinforced ribs/stiffeners can be incorporated during the manufacture of Shapeshell to reduce the number of components, hence resulting in a smart structure/design. Aluminum or steel connections with allowances for tolerances are typically incorporated into the design. Heavy collaboration with the architect/builder is essential to achieve an elegant design that is simple and fast to install.
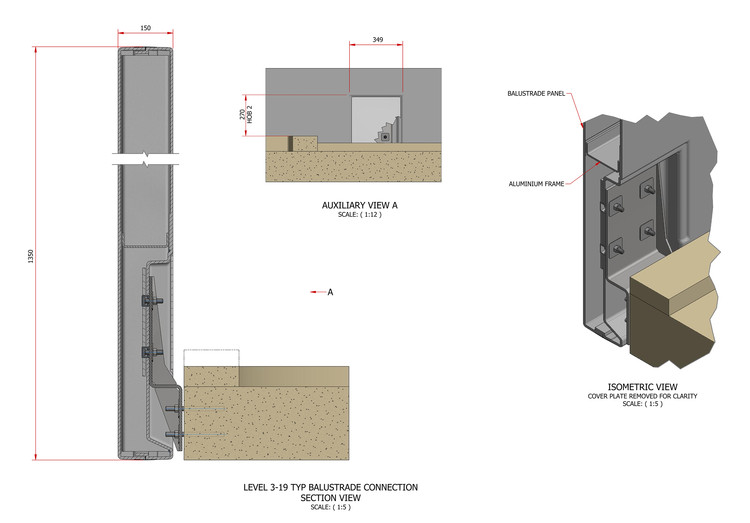
Technical characteristics include high strength-to-weight ratio, high impact strength, exceptional blast mitigation and low thermal conductivity.
Such properties are what initially led to the utilization of advanced fiber-reinforced materials within the aerospace and the harsh environments aerospace encompasses. Furthermore, as a non-reactive and non-conductive material, the difficult task of façade and structural maintenance for projects such as commercial high rises or high-density residential can be minimized over the lifetime of the building. The material is also recyclable, can be made with previously recycled materials, is more durable, and represents fewer embodied carbon miles due to its lightweight.
ShapeShell has been fire rated to both Australian and international standards (AS:5113-2016 and BS:8414, respectively), and offer multiple opportunities for customizability beyond the specifics of the product’s recipe.
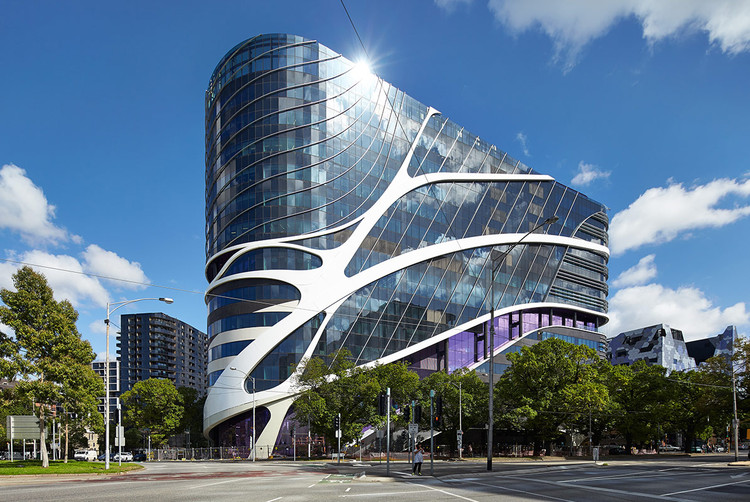
Surface finish can be customized as either a cementitious finish or a fluoropolymer finish and with a gloss level from 5 percent up to 80% within the full spectrum of colors. The use of fluoropolymer technology in coloring means that both the top layer and underlying matrix are colored, reducing the visibility of scratches on the surface. An anti-graffiti layer is also available as a customization option. The system as a whole offers a warranty of 50 years for the substrate, and up to 25 years for on the surface finish, including gloss retention. ShapeShell may also come in real metal finishes, including coatings that incorporate real metal nanoparticles such as tin, iron, steel, stainless steel, brass, and copper.
Now you can design a complex, light weight organic shape not possible in steel and achieve a real Corten finish that will age and behave the same as an aged steel plate. You can make a large number of shapes and the support structure will be minimal due to its light-weight nature.
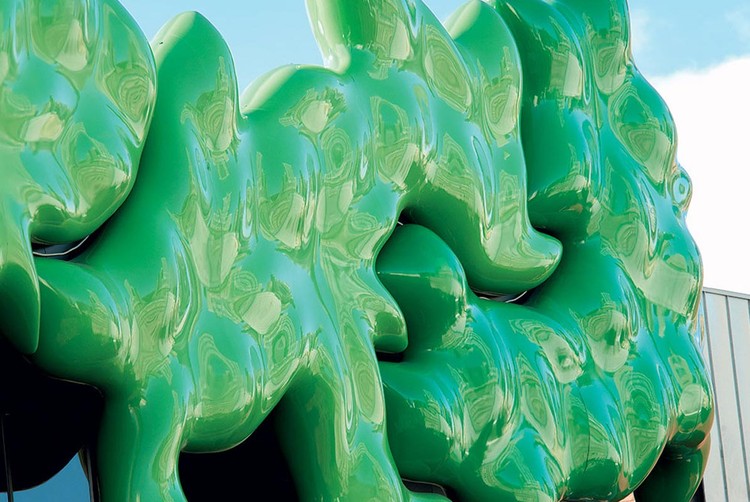
Queens Doman, multi-residential apartment complex
In this building, located at 12 Queens Rd, Melbourne VIC, Australia, the architect has taken advantage of the material as a balustrade system to emulate a precast finish.
Using a low post-tensioning of the slabs allow for a light-weight solution on the slab edge. Also, fewer columns in the building result in more space and visibility for residential apartments. Due to the overall light weight nature of the solution as a whole, the foundations were able to support an extra level the building, reducing number of containers for freight from our factory located off Singapore.
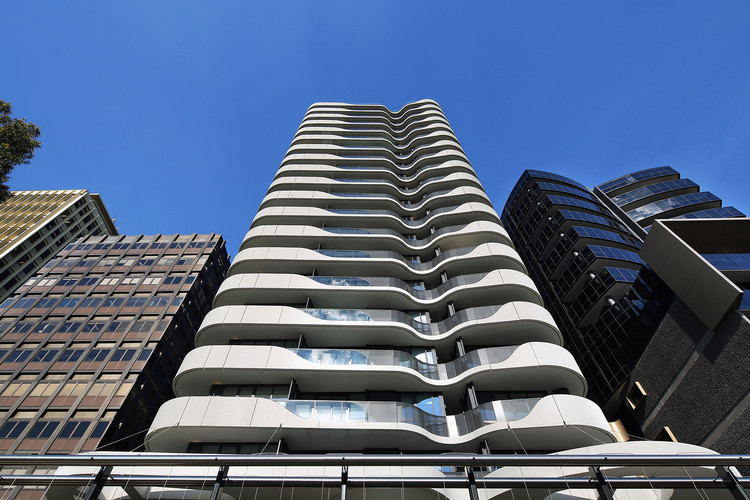

Orbis Facade
The result of applying advanced materials and digital design elements allowed the realization of Orbis Façade located at 99 Palmerston Crescent, South Melbourne VIC 3205, Australia.
This project turns the traditional building façade on its head and, in doing so, creates a unique series of manufacturing and construction challenges. Working with both negative and positive space, the façade projects into and out from the building structure – requiring an material that exhibits both light weight and enormous strength. The result is an extraordinarily dramatic “deconstructed” face not possible with traditional construction materials.